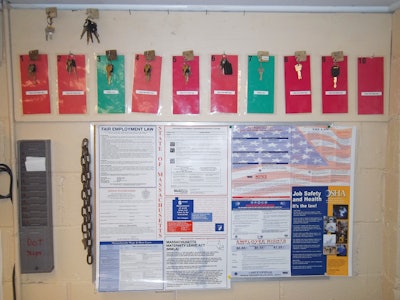
Hundreds of landscape companies have participated in the Working Smarter Training Challenge. Through this year-long training series, each has found ways to improve systems and processes—in the shop, in the field, and even in the office.
Getting crews out faster in the morning was something Tim Emick of Timberline Landscaping in Colorado Springs, CO, really wanted to improve. “We put someone on the roof of the shop to videotape our yard routine,” Emick tells. After reviewing the tape over and over, and consulting his account managers and foremen, Emick determined that improving the morning dispatch was primarily a matter of improving the evening arrival.
Start by organizing evening shut-down. “When crews come back to the shop in the afternoon, we now take extra steps to prepare for the next day by unloading excess waste, and loading up materials and equipment,” Emick says. This approach helps crews get on the road in a matter of minutes each morning. And since the laborious “housekeeping” tasks are handled at day’s end, when crews are eager to punch out and go home, they are handled quite expeditiously.
Mower blades are also changed at day’s end. “We set up blade-changing stations in the yard,” Emick says. “We poured concrete pads, and installed ramps, air impact guns and grease guns. Blades are now switched out and the mowers fueled up in a matter of minutes; less than half the time it used to take.”
The mechanic works “second shift,” punching in as the crews start arriving each afternoon, working into the evening hours. That way any equipment that’s in need of repair can be ready for the next morning (if at all possible).
Fueling up. Arnie Arsenault of A. Arsenault & Sons in Spencer, MA, says his crew members played a valuable role in identifying process improvements that have helped the company reduce the non-billable time spent fueling vehicles by 80%. Here’s what has happened:
BEFORE: After receiving their route sheet in the morning, the first thing crews did was head down the street to the gas station, whether they really needed gas or not. Two 2-man crews and two 3-man crews equals 10 employees—each wasting 10 minutes every morning. Total unbillable time: 1.5 hours per day.
AFTER: Now one employee comes in a half hour early each morning. He’s responsible for fueling up the trucks, equipment and gas cans. A “key board” hangs on the wall in the shop’s meeting room. Each truck has a hook and notification card; green means “fuel it” while red means “don’t fuel it”. When is it time to fuel a truck? When it’s below a half tank. Total unbillable time: 0.5 hours per day.
Dude, where's my crew? A. Arsenault & Sons has made one other important change. Crew leaders now come in at 7:45 a.m. to perform DOT inspections on vehicles, which is a big reason why the company’s fleet now runs a lot more smoothly. The crew members then arrive at 8 a.m. The first thing they do is look at the job board to see which crew leader they’re assigned to. This has eliminated confusion over scheduling and all of the wandering around associated with that confusion. “Our two-man crews are on the road in 5-10 minutes, and our three-man crews are gone in under 15,” Arsenault says.