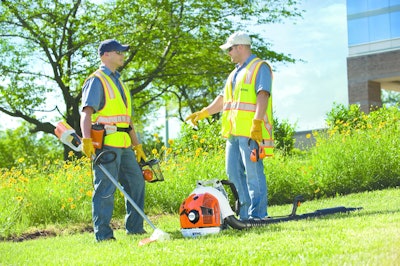
The Occupational Safety & Health Administration (OSHA) exists to help ensure worker safety throughout U.S. industry. OSHA does this through standards and regulations, educational outreach, and sometimes intervention, inspections and fines.
As PLANET points out in its "Safety Tailgate Training Manual", OSHA inspectors often drive by or visit jobsites to observe safety standards in practice. If they spot a violation—such as workers not wearing their recommended personal protective equipment, misuse of tools or other unsafe work practices—inspectors could issue citations and fines.
The best way to draw attention to your company is to have a workplace-related injury or fatality. But the inherent dangers associated with landscaping already place companies like yours in the spotlight. PLANET offers some suggestions to help prepare your company and its workers for a potential OSHA visit.
Every employee must be aware
Since impromptu OSHA visits typically happen out in the field on jobsites, step number one is to make sure all of your field employees, especially crew leaders, are aware. Everyone must understand what OSHA is and that there's a real possibility that an inspector could make an unannounced visit to a jobsite.
Of course, OSHA could also pop in at your facility. So any office staff, equipment mechanics or other employees should also be up to speed.
Setting the stage for a positive OSHA visit
Once employees understand that the possibility of an OSHA site visit is real, they must be trained on what to do to best ensure a positive outcome. PLANET offers the following tips, many of which speak to the creation of an overall safety culture within your company.
Keep jobsites neat and clean.
Always look for potential hazards. If an employee sees one, he must be trained to eliminate it or bring it to the attention of his supervisor, i.e. crew leader.
Always wear personal protective equipment (PPE).
Never disable, bypass or remove safety guards, shields or other devices from tools and equipment. If something to this effect is observed, the employee must be trained to immediately bring it to the attention of his supervisor.
Always follow all company safety procedures, plain and simple. But also be aware of the more frequent safety violations in this industry, which include: hazard communication (i.e. safety cones, warning labels on equipment, etc.), vehicle-mounted elevating and rotating platforms, eye and face protection, and head protection.
It's a good idea, as part of an overall yearlong safety training initiative, to stage mock OSHA inspections. Make sure all employees understand that these "practice sessions" are to be taken very seriously.
When an OSHA inspector shows up
Every field employee you have must be trained on what to do should an OSHA inspector approach a jobsite and ask to enter. Here's a simple process each employee should understand:
- Greet the inspector in a professional manner, depicting confidence and a desire to cooperate. Politely explain that the site supervisor (crew leader) then needs to be notified of the inspector's presence.
- Immediately notify the supervisor (crew leader) so the supervisor can greet the inspector and confirm the inspector's identity.
- The crew leader can then ensure that the inspector is provided the necessary PPE before entering the jobsite. (NOTE: This is another reason why it's a good idea to have a spare set or two of PPE in the truck, never mind the fact that workers sometimes forget something when you leave the yard in the morning.)
Sometimes an OSHA inspector will not just want to talk with the job foreman (crew leader), but also the workers on that job. Employees should always be polite and professional, but should also understand that they do not need to speak to the inspector if they don't want to. Make sure your employees understand this—which includes having confidence that you (their employer) won't punish them for not talking to the OSHA inspector.
Along those same lines, make sure your employees understand that they could request the presence of their supervisor (crew leader) while speaking with the OSHA inspector.
Finally, if an employee does choose to talk with the inspector, train the employee to always be honest. And if an employee doesn't have the answer to a question, make sure he or she knows that it's OK to say so.
Jobsite safety is a very serious matter, and OSHA exists to help reinforce that. Training your crews and other employees on how to handle an OSHA inspection should be part of an overall training effort in your company. This article will help you get a good head start. Contact PLANET for additional safety and training information.