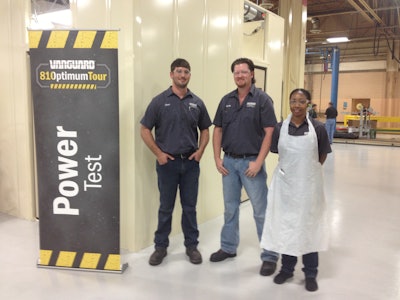
Briggs & Stratton recently hosted the Vanguard 810 Optimum Tour to introduce their new 810cc Vanguard engine designed to meet the needs of landscape contractors. In developing the engine, Briggs consulted commercial cutters and dealers. Voice of customer information was used to outfit the engine with the features Briggs says makes it the “ultimate ZTR engine”, able to withstand the demands of professional contractors. Much time and effort was put into the line before taking it to market.
“People make a living off these engines and we take that very seriously,” Joe Wright, Briggs & Stratton senior vice president and president of the Engines Group shares.
Engine details
In discussing the new Commercial Power Vanguard 810cc Engine line, Dan Roche, marketing manager for Briggs & Stratton Commercial Power, highlighted four main things that led to the Vanguard 810:
- Engine displacement is trending up to greater cc
- Engine compartment footprint is not changing
- New safety standards impact design (ANSI B71.4 safety regulations)
- Built for durability and reliability, paired with three-year warranty
Features that provide the durability and power contractors desire include a new debris chopper fan designed for improved debris management that provides up to 30-degree cooler engine temperatures. Debris access panels allow for quick and easy engine maintenance. The high-flow blower housing offers more than 30% larger intake surface area than the next closest competitor, Briggs reports.
Building in Auburn
In deciding where to manufacture the new Vanguard 810cc engines, the company decided on its Auburn, AL, factory. This will be the first commercial engine from Briggs to be built in America, though 85% of Briggs engines are already manufactured in the U.S.
The Auburn location was chosen for a number of reasons. Briggs wanted to be close to mower manufacturing customers, and close to their engineering muscle. Briggs believes this choice will help with customer response time and product planning. The popular V-twin engines are also built at the Auburn location.
“Our goal is to build on the V-twin focus,” explains Dave DeBaets, vice president of North American Operations, when discussing their engineering processes. “We have the technical skill and experience dating back to 1995.”
A craftsman approach to building
Briggs & Stratton wanted to take the craftsman approach to assembling the Vanguard 810 engine, not treating it as a mass-produced product. A small, elite team of three Master Service Technicians (MSTs) work together closely to build and test the engines.
MST status is reached after extensive study and testing. In designing the manufacturing line, the MSTs were consulted on the tools and layout. In building the engines, the MSTs use several Direct Current (DC) precision tightening tools that will track the torque of each turn at the engine’s critical joints. Each turn is logged with the individual engine barcode.
At the end of the line, each engine is load tested. As certified MSTs, the Vanguard line employees are able to diagnose and repair any issues before the engines leave the line. The line is currently producing 15 engines a day, and will be up to 100 per day in January. There is also room for the anticipated expansion of Vanguard 810 line at the Auburn plant.
Several mower manufacturers have signed on to include the new engine in their line. Those companies will be revealed at GIE+EXPO where Briggs says the engines will be seen on mowers in several booths.