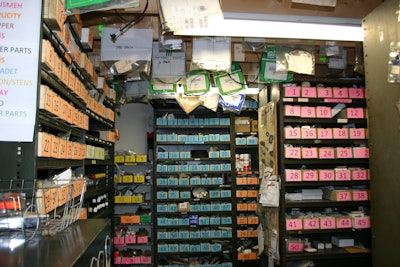
One of the major concerns John Deere is hearing from its customers is that it’s often difficult to maintain an efficient parts department. Professional landscape contractors (PLCs) often fail to properly manage their parts inventory, leading to parts being used without awareness and not available when they are needed. For PLCs, this is detrimental to their businesses because it leads to downtime, which hurts their bottom lines.
John Deere can help PLCs better run their business with these six suggestions for maintaining an efficient parts department.
1. Assigning inventory ownership. By limiting the number of employees with access to parts storage, contractors can diminish the risk of parts being used without being tracked. With one person overseeing the parts department, it ensures efficient management of the inventory, thus eliminating downtime.
2. Organize and label bin locations. It’s important to create designated part storage locations with labels so the manager is aware of where things are and what needs restocking. The minimum stocking level should be included on the labels so when parts are reordered they can quickly identify how much to order.
3. Track parts usage by machine. Unscheduled maintenance and repairs can be a big blow to any contractor’s budget. It’s recommended that PLCs track what parts were used for each machine and the cost per part. This can help identify the repair cost for each particular model and help determine whether companies should repair or replace a piece of equipment. By understanding the service intervals and required parts throughout the year, PLCs can efficiently plan and have the necessary parts in stock at their location.
4. Create an immediate tracking process. While it may seem tempting to wait until the end of the day to track the parts that were used, it actually increases the chances that a part will be used without notice. Establish an immediate tracking mechanism to limit the risk of forgetting a part through work orders or spreadsheets.
5. Schedule regular inventory reviews. While it doesn’t need to be quarterly, it’s important to review parts inventory on a periodic basis. Use this time to examine what is being used and adjust minimum levels accordingly. Add or remove parts that are needed or not needed anymore. If new machines join the fleet, PLCs need to make sure they have the right parts. As fleets grow, so does the need for parts.
6. Consider financing parts. Manufacturers often offer deals to help PLCs finance parts to help free up cash. Be sure to check with your dealer to see what types of offers may be available.
A parts management system doesn’t need to be overly complex to be successful. By following these simple tips PLCs can limit downtime and keep their businesses up and running.