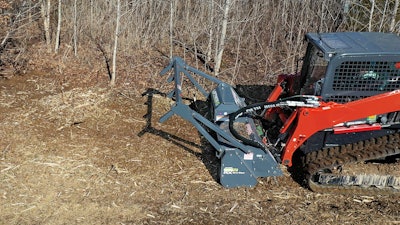
Mulching heads, or forestry mulchers, are popular attachments for skid-steers and compact track loaders. They’re a great option for quickly taking out unwanted vegetation and sizing it for fast decomposition. The job won’t get done so quickly, however, if the attachment isn’t used correctly. Below are some tips to maximize performance and help you get the most out of your mulcher.
Get the right fit
The first step to success with a mulching head is to make sure it’s compatible with the power unit. Three of the biggest factors when selecting a mulching head are hydraulic horsepower, weight of the power unit and width of the mulching head.
Hydraulic horsepower
When it comes to finding the right mulching head for a skid-steer or compact track loader, hydraulic horsepower is much more important than engine power. To determine hydraulic horsepower, simply multiply the GPM and PSI of the power unit’s hydraulic system and then divide that number by 1,714. For instance, a track loader with hydraulic ratings of 36 gallons per minute at 3,450 PSI would have a hydraulic horsepower of 72.5 (36 x 3450 / 1714).
Mulching heads are available for a wide range of skid-steers and compact track loaders, even lower-flow models. Keep in mind, however, that performance is directly related to hydraulic power. A low-flow skid-steer won’t be able to keep up with a high-flow skid-steer. Likewise, a skid-steer that is on the low side of the hydraulic horsepower requirements for a mulching head may not match the performance of a more powerful skid-steer at the higher end of those requirements.
Power unit weight
Before purchasing a mulching head, it’s important to ensure that the skid-steer or track loader has the weight capacity to carry it. Also, consider the working conditions. Flotation can be an issue with some power units when a heavy mulching head is used on soft ground. The weight and balance of the unit makes stability another consideration when operating in rough terrain, steep hills and valleys.
Cutting width
One factor that’s often overlooked when purchasing a mulching head is the cutting width. While it’s true that a wider head can cover area more quickly than a narrower head, it may not accommodate the ground contour as well on some jobsites. For instance, in narrow ditches, a 5-foot-wide head will likely be able to cut lower to the ground than a 6-foot-wide head can.
Cutting width also ties back in with hydraulic horsepower. If a person is concerned that his skid-steer or compact track loader is on the low end of the hydraulic requirements for a mulching head, it may be wise to select a narrower model over a wider one. That’s because it simply takes less power to spin a narrower rotor than a wider one.
Other important considerations when selecting a mulching head are the cutting teeth and rotor options. Many mulching heads can be used with either carbide teeth or sharpened knives. Carbide teeth are a durable, low-maintenance option for inexperienced operators, and they are usually recommended for rocky conditions. Lately, however, more operators have been gravitating toward sharpened knives. Although knives are not as durable and require regular sharpening, they are much more aggressive, making them capable of cutting finer and working faster than carbide teeth.
The cutting teeth decision leads into a discussion about the rotor. As sharpened knives have become more popular, so have limiting rotors. Because knives have a natural tendency to bite into material more aggressively than what is ideal, a limiting rotor helps control the material infeed for more efficient performance. The two main types of limiting rotors available today are ring style and depth gauges. Ring-style rotors are generally known as having the most restriction. Depth gauges aren’t quite as restrictive, which allows operators to pick up material from the ground more easily, especially when using less aggressive carbide teeth.
Working under pressure
When operating this equipment for the first time, one of the most important pieces of advice is to understand the power unit’s hydraulic capabilities and then to stay within that range. Generally, it’s recommended to operate 500 PSI underneath the maximum hydraulic relief pressure. For instance, if the skid-steer or track loader has a maximum hydraulic relief pressure of 3,500 PSI, then the operator should try not to exceed around 3,000 PSI.
Most mulching heads have a pressure gauge on the top of the unit for easy reference. The pressure goes up as the load increases, and the rotor will slow or even stall when the maximum relief pressure is reached. When this happens, performance is decreased, and heat is generated, which could potentially cause damage to the hydraulic system. To reduce the amount of pressure, operators can decrease driving speed and/or engage material more slowly.
More than one way to mulch
There are several ways a mulching head can be used. First, the head can be tilted back to expose the knives for felling standing trees. Next, operators can shave off large material from a felled tree by lowering the rear of the unit to contact the trunk, which prevents logs from being ejected to the rear.
Another application is forward mulching. When doing this, the rear of the cutter can be lowered close to the ground to help trap material in the cutting chamber for more thorough processing, if desired. Some mulching heads have adjustable skid shoes for height control, which can even be set for mulching below grade.
Operators can also reverse mulch or backdrag. Here, the head is tilted forward while the skid-steer or track loader backs up. This is very effective for sizing material since this action pulls the downed material against the cutter bar and into the chamber. Some units have an adjustable cutter bar to help control particle size and production rate. Some units also have a second cutter bar behind the front bumper, allowing material to be cut twice for more thorough processing. This feature is often referred to as a two-stage cutting chamber.
When running a mulching head, many operators take a two-step approach. First, they drive forward on an initial pass to reduce material to ground level. The objective here is to quickly knock material down without processing it thoroughly in the head’s cutting chamber. Then, they backdrag to size the material down for faster decomposition and/or create a nicer looking end product. Of course, only the first step needs to be taken if operators aren’t concerned about sizing the material down. This approach can dramatically improve your production rate if the customer is content leaving larger pieces to rot on the ground over longer periods of time. In the end, how a mulching head is used will largely come down to the type of job and client requirements.
Of course, experience is the other component to maximizing performance. After several hours behind the wheel or joysticks, you’ll eventually get the hang of things and start working your way toward becoming a master mulcher, but this advice, combined with support from your equipment dealer, will help give you a good head start.