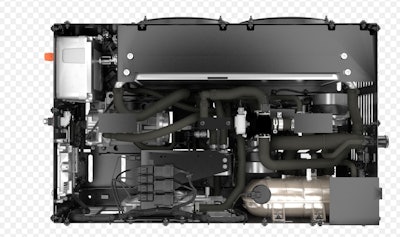
The coming months present an ideal opportunity to adopt and integrate new technologies to improve their fleet of snow removal machinery before bitter temperatures and frosty weather conditions return.
While the e-mobility revolution has transformed the transportation landscape for passenger cars, buses, trucks and more, the electrification of snow removal vehicles remains slow. Like the early stages of electrifying medium- and heavy-duty commercial vehicles, snow plows encounter unique challenges in transitioning to electric power due to their intricate operation and specialized requirements. For instance, these vehicles must be prepared to run for extended periods, navigate harsh, freezing conditions, and consistently deliver the power required to perform their intended tasks effectively. As such, developing an electric solution that matches the reliability of diesel-powered snow removal equipment has proven challenging, with just 9% of operators exploring energy-efficient electric or alternative-fuel equipment for their snow plow fleets in recent years.
An electric snow plow contains many systems that are unique to internal combustion engine (ICE) snow plows, and incorporating thermal management systems into an electric snow plow is paramount to the success of its operation. All commercial electric vehicles contain lithium-ion batteries and power electronics. Keeping these vehicle systems at their optimal temperature determines the success of a snow plow’s work day. Lithium-ion batteries in EVs degrade and lose efficiency under harsh environmental conditions on both ends of the mercury, making precise temperature control essential for their reliable operation. In the unique case of snow plows, which operate exclusively in freezing environments, maintaining an optimal temperature range is challenging and critical for avoiding performance issues within electric units.
Fortunately, decades of innovation in vehicular thermal management have led to the development of advanced technologies, such as cooling and heating circuits equipped with sensors and sophisticated control systems to regulate EV battery temperatures consistently. These advancements have enabled EVs of all sizes, including electric snow plows, to operate effectively even in the most severe weather conditions.
Battery thermal management explained
Though often overlooked, battery thermal management is crucial in EVs, as ambient temperature significantly influences vehicle range, charging speed and battery longevity. For optimal performance during the dual demands of charging and operation, battery pack temperature should ideally remain between 68 degrees F to 113 degrees F. Therefore, a battery thermal management system (BTMS) must be able to heat and cool the battery pack it manages. If ambient temperatures drop too low, the BTMS heating loop will warm the coolant to elevate the battery pack temperature to the preferred range. The BTMS will remove heat from the battery pack while operating or charging to prevent overheating. The system's automatic control over cooling and heating, including how intense each mode operates, reduces complexity for fleet operators and drivers.
A key consideration in BTMS design is optimizing temperature control while minimizing power consumption. Snow plows require an excessive amount of power to operate efficiently. Beyond maneuvering the actual blade, a snow plow will typically engage its windshield wipers, headlights, heater, radio and more simultaneously, all of which consume additional power. Electric models must carefully monitor power distribution to ensure the vehicle can sustain extended shifts while handling these extra functions.
Broader thermal management considerations
The various inverters, converters, traction motors and related power electronics that charge the batteries are similarly impacted by ambient and operating temperatures. Due to their weight, payloads and workloads, electric snow plows demand substantially higher power from their powertrain electronics than typical light-duty or passenger EVs. Increased power results in higher heat generation, which stresses electrical components more, leading to a greater risk of compromised performance, durability, and longevity. In the case of inverters, for instance, power output is limited by the maximum temperature threshold of the power module, affecting performance and potentially causing shutdown without intervention from a thermal management system.
Electric machinery such as snow plows need to be outfitted with a cooling package for inverters, converters, traction motors and onboard chargers each employing a coolant loop to regulate the temperature of power electronics. This circuit keeps the power electronics within the temperature range, which ensures the best performance and the lowest risk of damage to sensitive components. In many applications, such as during a heavy snowstorm where uninterrupted operation is crucial, dependable thermal management of drivetrain electronics safeguards both the asset and the critical operations it supports.
Preconditioning preparations
Like many commercial electric fleets, managing an electric snow plow fleet presents a distinct challenge. Fleet managers must effectively strategize charging times and routes to prepare vehicles for deployment, necessitating the development of a robust preconditioning strategy. This strategy involves ensuring vehicles are charged adequately and optimizing their readiness for harsh winter conditions.
Preconditioning involves heating a vehicle's battery to the optimal temperature for maximum operation, ideally done while the vehicle is connected to a charger. Like a snow plow, a large earth mover requires larger battery packs, resulting in more thermal mass. Storing heavy-duty EVs like snow plows in climate-controlled depots is recommended to maintain ideal battery temperatures. Without access to heated indoor parking, larger battery packs take longer to reach ambient temperature equilibrium, thus extending the time required to warm them back to optimal operating temperature. In these cases, a robust BTMS is essential for the success of the electric fleet.
Connecting to a charger whenever stationary, especially in cold weather, also allows a BTMS to protect the battery pack and mitigates the risk of a cold-battery performance reduction of up to 40%. Moreover, nearly two-thirds of range reduction in cold weather stems from the battery draw from cabin heating. To extend the range between charging sessions, fleet managers should advise drivers to use in-cabin comfort features like heated seats and steering wheels when necessary while turning off heaters when the vehicle is not in use.
Forging the path forward
Effective thermal management is the linchpin for the future success of electric snow plows. With the strategic integration of robust BTMS and power electronics cooling packages, electric snow plows can overcome the unique challenges posed by extreme weather conditions, ensuring sustained performance, unwavering reliability and operational longevity. As more innovations emerge and best practices are refined, the trajectory of electric snow plows appears increasingly promising, heralding a future where clean, efficient and resilient snow removal solutions become the norm.