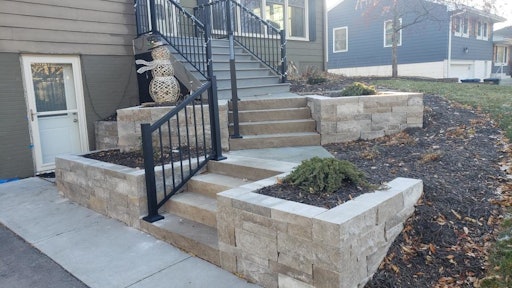
When a client wanted to elevate the curb appeal of their front yard, Ground One Landscape Design + Build + Maintain rose to the challenge.
Overall, the project included natural stone retaining walls, bluestone paving and a revamped deck, according to Robert Latham, landscape designer at Ground One.
The first part of the project, Latham says, involved replacing old timber walls that separated the driveway from the front door, which was 7 feet higher than the driveway and garage door.
“It’s a split level, and the timber walls were failing, so our design team was tasked with developing a solution to restore functionality while enhancing the overall aesthetics,” Latham says.
Before demoing the timber walls, crews saved a few of the existing hydrangeas. After the demolition, crews added in a few more plantings and constructed several Indiana limestone steps that ran up and met with a composite staircase to create a landing near the front door.
“Our crews are really well-versed in working with natural stone, whether it be working with a mortar setting or a dry stack installation, and these walls are dry stacked,” Latham says.
Latham adds that the company subcontracted out the construction of the deck.
All in all, four to six Ground One employees (including the designer, project manager and crews) worked over the course of a month to complete the project.
A huge component in bringing the design to life, Latham says, was a Vectorworks app called Nomad that features light detection and ranging (LIDAR).
“When we go to collect our site inventory, we’ve been using our iPhones because they have a LIDAR-enabled camera to collect 2D and 3D information,” Latham says. “It gives you a pointcloud to work with that we can directly import into our file and quickly start to understand the space in 3D while we’re drawing up a 2D plan.”
Latham says the company also used an altimeter to gain additional elevation data or a laser level.
When it came to the production side, the company used a skid-steer loader to load and unload materials and then moved debris, mulch and plant material using shovels and wheelbarrows.
While the majority of the project went off without a hitch, Latham says the company did have to take extra care to coordinate with the subcontractor to correctly match up the composite landing with the decking.
“With a lot of the work we do, there are usually a bunch of different professionals that are on the site at any given time,” Latham says. “It’s better if we can coordinate to have our work completed.”
On the same note, Latham says communication remained top of mind for everyone involved on the project—including the design department, bidding department, production staff, crew members and subcontractor—and the 3D renderings were a huge facet to that ability to communication.
“It makes it easier to communicate about the intent of the project, what materials are used and how to work together more effectively,” Latham says. “It’s about keeping open minds and trying to have an elite corporate environment because there are just so many moving parts in what we do.”