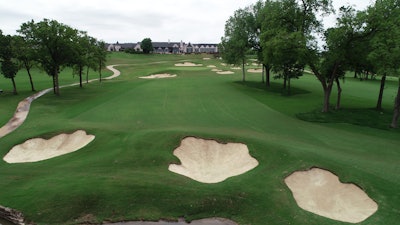
You don’t have to wipe the slate clean to be innovative. New trails can be blazed by complementing, building on and coexisting with the best parts of an original invention.
Southern Hills Country Club in Tulsa, Okla. is committed to bringing both its historic traditions and modernizations into the future. That’s why they were so excited about architect Gil Hanse’s master plan. It called for restoring some of the original features of the championship golf course Perry Maxwell designed during the Great Depression in 1936 and enhancing that with the latest in hydronic turf technology and irrigation.
Closed since August 2018, the course reopened in June following a $19 million facilities project that devotes $11 million towards the golf course.
Improvements include a 3-hole short game area, indoor golf performance facility, an underground bag and cart storage building along with new greens, bunkers, tee boxes, cart paths and the installation of a hydronic heating and cooling system for the putting greens.
“Providing the best experience for members of Southern Hills is essential,” said Russ Myers, SHCC’s golf superintendent. “This allows us to improve course conditions in stressful weather.”
Players will now experience the best of the past and the present on a course that stands firm on the world stage as a site for major championships. Since 1946, they have hosted 15 major championships — the last being the PGA Championship in 2007. Next up is the Senior PGA in 2021.
There were as many as 96 people working onsite during any given day of the construction. The club had its own crew of about 32 people and the other workers were from Heritage Links, the general contractor, and Formost Construction Co., the hydronics and irrigation contractor.
A Maxwell restoration with a modern edge
Maxwell was influenced by courses in Scotland that were designed in harmony with the existing landscape. His bunkers were built by hand, horses and plows as opposed to bulldozers which have a tendency to flatten the landscape. Hanse used excavators with adjusting angels and varying heights of sod on the edges to create Maxwell’s more natural look and movement.
“There wasn’t this clean, circular look to the bunkers originally,” Myers said. “You see more movement of the line — it doesn’t just run in a perfect saucer.”
Old aerial photos were used to pinpoint the original locations of the bunkers, tees and drainage areas, and they were able to restore some of the original creeks including one on the 10th fairway.
“The creeks on this golf course may be like no other in the state and is on par with anything you’ll see in the country,” Myers said. “People come to golf courses and look at conditioning and trees but often don’t pay attention to the routing and subtleties like the creeks and this place has that in spades so that’s pretty special.”
The restored course stays true to the spirit of Maxwell’s work as much as possible. The fairway bunkers on 1, 12, 15 and 9 aren’t Maxwell’s, but still exist because people hit the ball much farther in today’s game. Overall, Myers said the course is a nice homage to Maxwell’s work while adapting to the needs of the modern game.
Creating the perfect growing conditions
The greens were redesigned and rebuilt to survive the scorch of an Oklahoma summer and the chill of a harsh winter. WattsRadiant PERT tubing was installed under the greens to cycle cool or warm water, keeping the surface at the optimal temperature for sustaining the preferred, cool-weather creeping bent grass. The greens sustained significant damage in three of the last nine summers. The hydronics solution is designed to trick the grass into the best June and September growing conditions.
“That’s a 33 percent impact during the summer months and that’s pretty big. If we can take that away, that’s a huge benefit,” Myers said.
Heritage Links started with a 4” foundation of pea gravel for drainage. On top of that is the ¾” tubing in 9” spacings. The top is a USGA-specified 12” mix of sand and peat and the greens are seeded on top of that.
Fusing it all together
The tubing connects to a manifold buried outside the green which is connected to an extensive supply and return system made of high-density polyethylene pipe, a non-corrosive pipe material that is joined with leak-free fusion technology. In all there is about 30 miles of HDPE pipe in sizes from 2” up to 20” to irrigate the course.
“Everybody is going with HDPE because it’s more reliable and lasts longer. All the bigger courses are going with that,” said Formost Administrator Matt Johnson.
Part of HDPE’s dependability is the joining method through heat fusion. This is created by joining two ends of pipe together with heat and pressure which causes the flow of melted material. As the joint cools, the two pipes become one monolithic pipe. To insure a quality fusion, it’s important to use quality fusion equipment. This job featured held-held socket tooling and rolling machines made by McElroy.
Johnson said they are able to buy or rent McElroy equipment wherever they’re working across the country and training for all their pipe fitters is readily available with McElroy distributors. With McElroy, they’ve been able to do the job right ever since they first started using HDPE on golf courses more than 30 years ago.
“If the equipment wasn’t doing the job, we wouldn’t use it,” he said.