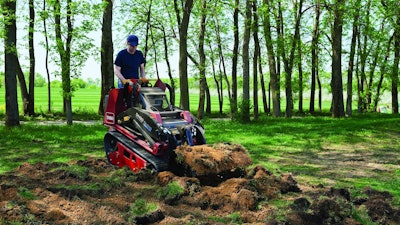
Take a look at almost any jobsite these days and you’ll likely see compact tool carriers (or CTCs). The equipment is popular because of its versatility and its maneuverability, even in hard-to-reach areas. Productive equipment like CTCs make for a productive jobsite, so it’s essential to have a comprehensive preventive maintenance plan in place to keep them operating at peak performance.
Five Basic Steps
It’s better to be proactive than reactive. If you wait to perform service until after equipment has failed, you’re stuck with downtime. But if you schedule maintenance in advance, you can plan your work schedule around it. Plus, preventive maintenance is much easier and much more cost-efficient than major repairs.
Here is a five-step preventive maintenance plan for compact tool carriers.
- Visual Inspection: Eyes and ears can be the best tool, so use them by searching the CTC for any signs of damage, noise, rattles or wear. Start by inspecting the tracks or wheels, nuts, bolts, body, controls, guards, and any attachments. Look for any leaks around the hydraulic fittings, hose chaffing, and fuel hose. Check the battery for corrosion on the terminals or any loose or fraying wires. If the battery terminals need cleaning, remove the negative terminal first and re-install it last. Check the tire pressure or track tension. Inspect the belts and replace any that show wear or cracks.
- Maintain Fluid Levels: Most operators know to check the engine oil and coolant, but it’s also essential to be sure that hydraulic fluid levels are where they’re supposed to be. If necessary, top them off while being careful not to overfill. If the hydraulic fluid has a milky color, that’s a sign that there is water in the system. The hydraulic oil will need to be changed immediately because as the machine heats up, water in the system will turn into steam that can cause serious damage to the pump and wheel motors.
- Clean Filters: Restricted airflow can reduce performance and lead to engine damage, so the air filter will need to be inspected and changed on a regular basis. It consists of the canister, indicator, and main filter. Some air filter systems are fitted with a service indicator mounted outside of the canister. The service indicator is the first indication of the air filter condition. If the filter is restricted, the inside indicator will block the clear viewing window. Be sure to clean the outer prior to opening it to inspect or service the pre-filter or the main air filter. To meet recent EPA standards, many engine systems now have a component called a carbon canister, which collects fumes from the fuel systems. The carbon canister has a service life and needs to be replaced every 200 hours or sooner if the canister becomes restricted with dust, dirt, or saturated with fuel. Hydraulic filters need to be replaced every 200 hours or if the hydraulic oil is contaminated. When replacing hydraulic or any filter is recommended to use the OEM filter to assure the proper fit and meets the OEM specifications.
- Lubricate Properly and Tighten Connections: Many problems occur simply because a part is loose. Performing a simple check with visual inspection and touch the object to verify if loose or broken, tighten with a wrench before using your CTC compact tool carrier will reduce wear and extend the life of the machine’s components. Grease all pivot points and tighten all nuts and bolts before heading out into the field.
- Safety Check: Make sure the parking brake is engaged (if applicable) and that the traction control lever is returned to neutral. Also, make sure that auxiliary hydraulics are disengaged, as many compact tool carriers will not be able to start the engine if the traction control and/or the auxiliary hydraulics are not in the neutral position.
The Dingo TX 1000 Wide Track. From earth moving, tilling and trenching to leveling, lifting, hauling and demolishing, all Toro Dingo models can be equipped with over 35 attachments to handle an endless amount of tasks.The Toro Company
Preventive maintenance isn’t a chore so much as an investment. A small amount of time spent caring for your CTC will save you the significant lost time, money, and productivity of a major repair. You’ll also save by getting more hours out of your equipment and needing to replace it less often.
Scheduling Your Maintenance
Now that we’ve covered what to do, let’s look at when to do it as well as more in-depth maintenance. By keeping track of your CTC’s usage hours, you can follow this schedule:
Every 25 Hours
Clean the foam air filter after every 25 hours of use. They are essential components that must be maintained for the equipment to perform at its best. Because compact tool carriers are used in the roughest of conditions where fluid connections can come loose or hoses can be damaged, this is also a good time to take a good look at the hydraulic lines and make sure that they aren’t leaking. Small hydraulic leaks can quickly grow into larger and more expensive leaks, so it’s in your best interest to have leaks repaired when found.
Every 100 Hours
You’ve been cleaning your air filter every 25 hours, but now it’s time to replace it. A deformed or torn air filter will allow dirt to pass into the engine and can potentially cause substantial damage. And just like anything with an engine, the oil needs to be changed regularly, and every 100 hours is a good interval. Also, inspect the fan belts and replace any belt that is showing signs of glazing or cracking.
Every 200 Hours
In addition to again changing the air filter and engine oil, now is the time to replace the engine oil filter, hydraulic filter and fuel filter as well. Take a look at the spark plugs, too, to make sure they aren’t worn or fouled. Review the condition of the porcelain and get rid of any spark plugs that are cracked or in a questionable condition. If your CTC is diesel-powered, make sure the glow plugs are operating to ease the starting of the engine.
Every 400 Hours
By 400 hours of use, your CTC has come through for you time and again. Reward it with a little extra care. Start by checking the engine speed. This can vary from machine to machine, so be sure to check the manufacturers’ specifications in the owner’s manual. It’s also time to replace the belts and check the condition of the tires or tracks. Tires should be replaced when the tread is worn down, or the rubber is cracked. Tracks should be replaced if there is any apparent damage to the rubber or if the lugs are worn.
Refer to the Operator’s Manual for additional information to keep your compact tool carrier operating at peak performance for a long time. In addition to increasing the return on your investment, you’ll keep your crew productive and help reduce unexpected downtime on the job.
Dan Roberts is a Sr. Technical Service Representative for The Toro Company.