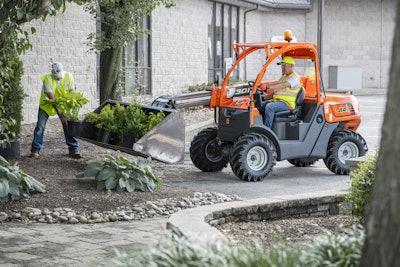
Managing equipment in the green industry is no small feat. Whether you're in landscaping, turf maintenance, arboriculture or irrigation, your machines need to be where they’re supposed to be, running efficiently and ready for action. But rising costs, complex jobsites and limited labor have made fleet planning and lifecycle management more needed than ever.
Fortunately, the Internet of Things (IoT) is changing how green industry businesses handle their equipment, from acquisition through retirement. No longer just about tracking a dot on a map, IoT is evolving into a full suite of solutions that enhance visibility, reduce downtime and help crews do more with fewer resources.
Rising Equipment Costs Demand Smarter Usage
As equipment prices rise, supply chain issues persist, and demand for cleaner technologies grows, green industry businesses are under pressure to extend the life of their assets and maximize value from every machine.
Modern IoT-enabled equipment helps tackle this challenge by embedding connectivity at the manufacturing stage. That means machines arrive on the job ready to transmit data, with no need for manual activation or third-party installation. Once powered up, these systems begin collecting runtime hours, diagnostics, and usage patterns immediately, giving subscribed equipment managers the tools to track performance, flag maintenance needs, and prevent overuse that shortens service life.
This seamless onboarding reduces friction and ensures equipment starts delivering operational insights from day one.
Sustainability Goals
Many clients now expect green industry contractors to meet sustainability standards or prove they’re reducing emissions and fuel use. That’s difficult to do without reliable data.
IoT systems offer this visibility by recording how machines are being used, when they’re running, how long they idle and how efficiently they operate. This allows companies to adjust work schedules, rotate machines more evenly and adopt sustainable operating habits based on real-world insights.
Underutilized Equipment Hurts the Bottom Line
It’s common in the green industry to hold onto more equipment than necessary “just in case.” But machines that sit idle too often are quietly draining profitability. Without clear data, many companies over-purchase or under-deploy their assets.
Connected fleet systems offer a real-time snapshot of machine usage across all jobsites. By identifying which equipment is actively being used — and which isn’t — companies can rebalance their fleet, sell off underperforming assets or rotate machines more effectively to reduce wear on high-use units.
Labor Shortages Mean Automation Matters
The ongoing labor shortage is hitting the green industry hard. With fewer hands available, operational efficiency has become critical. That includes minimizing the time it takes to locate, service or manage equipment.
IoT platforms may include features like audio-visual locators (lights and beacons triggered by mobile devices), which drastically cut the time it takes to find a machine in a busy yard. Bluetooth mesh networking also allows nearby machines to communicate with each other, so even if cell service is poor, crew members can still find, connect to and work with the right equipment without delays.
Some professionals estimate that locating a machine manually can take up to 45 minutes, especially when multiple similar units are parked in rows. With IoT, that same task can take just a few minutes, saving valuable crew hours every single day.
More on telematics from GreenIndustryPros.comTelematics in Action - Landscape professionals discuss how they best leverage GPS + telematics technology to their advantage. Telematics go Beyond Fleet Management - Continued advancement in telematics technology is bringing about more data collection and predictive maintenance capabilities for OEMs and end-use customers. How Smart Service Businesses Use Telematics Data to Build Winning Teams - This e-book explores how successful fleet-based service businesses leverage GPS and telematics data to train, oversee, and retain high-performing teams. |
Too Much Data, Not Enough Usability
A common complaint about early telematics systems was information overload. They offered reams of raw data but little usable insight. Many businesses gave up on these systems because they required too much time and effort to interpret.
Today’s IoT tools are designed to be intuitive. Instead of separate subscriptions or serial-number-based management, many platforms now bundle connectivity into a single fleet-wide agreement. That removes the need to track individual start and end dates or worry about whether a specific machine is “on.” Everything just works, and updates are delivered automatically.
The focus has shifted from collecting more data to making the right data visible at the right time, in an interface that's accessible from both mobile devices and desktops.
Delayed Maintenance Creates Downtime
In the rush to meet project deadlines, maintenance often takes a back seat. But reactive repairs are far more expensive and disruptive than proactive service.
With connected systems tracking usage hours, fault codes and diagnostics in real time, maintenance scheduling becomes proactive rather than reactive. When paired with mobile access, service personnel can perform diagnostics, troubleshoot or change parameters using digital-enabled solutions, such as Bluetooth analyzers and analyzer readers, to reduce downtime and improving machine availability.
Tracking
Whether it's equipment being rented to third parties or shared across crews, keeping track of a machine's location — and determining whether it should still be there — can be a logistical challenge.
IoT platforms solve this by tracking movement and usage over time. If a piece of equipment is supposed to be returned or pulled from service but is still being used, the system can flag this immediately. Asset recovery becomes faster, simpler, and more accurate, making sure equipment isn’t lost in the shuffle.
Instead of waiting for a machine to go missing, managers have real-time insight and can respond proactively.
Green industry jobs often take place across large or remote sites where GPS alone can’t pinpoint machine location. Traditional telematics might tell you a machine is “in the area,” but not where exactly, especially when buildings or terrain interfere with signals.
Automated site networks enhance site-level visibility by allowing machines to form their own localized communication clusters. As machines move into or out of the network, check-in and check-out events are automatically logged. Crews can see exactly what equipment is present at a given site, even without cell reception.
This is especially useful for fleet managers supplying equipment to projects in multiple locations. They can filter by site, zoom in on specific machines, and track movement without physically being there.
Documentation & ROI
For companies working with municipalities or regulated sectors, proper documentation of service history, usage logs, and diagnostics is often mandatory.
IoT systems simplify this by leveraging digital technology that provides a more robust, comprehensive picture of an asset or fleet. In the future, as more systems communicate with one another, you can start seeing a cloud-based, time-stamped history of all machine activity. For example, maintenance records, fault codes, and runtime hours could be automatically logged and exported, eliminating manual paperwork and helping green industry crews stay compliant with safety and environmental standards.
Making smart financial decisions, like when to service, rotate, resell, or retire a piece of equipment, requires more than just knowing how old it is or where it’s located. For green industry professionals, especially those integrating electric or hybrid equipment into their fleets, lifecycle planning now depends on capturing and analyzing a new set of performance metrics.
Electric-powered machines demand different insights than their fuel-based counterparts. Key data points include voltage levels, battery run cycles, charge rates, state of charge, and charge retention over time. These indicators are crucial for understanding true machine health, predicting battery life, and scheduling maintenance or replacements to prevent downtime.
IoT platforms that can collect, interpret,t and present this type of equipment-specific data, rather than simply aggregating generic engine hours, enable more accurate, real-world lifecycle decisions. Subscribed equipment managers can identify machines that are performing optimally, flag underutilized or energy-inefficient units, and estimate remaining useful life based on actual battery and usage conditions.
Ultimately, it’s not about collecting more data — it’s about having the right data. Over time, this leads to smarter capital investments, reduced maintenance surprises, and better returns on equipment costs in both traditional and electric fleets.
Put Into Action
The green industry is moving faster and operating leaner than ever. Whether a business is managing a handful of machines or hundreds across multiple crews and sites, IoT technology offers a better way to understand, manage and optimize an equipment fleet.
By reducing guesswork, automating time-consuming tasks, and delivering actionable insights, connected fleet systems empower green industry pros to solve their biggest lifecycle challenges efficiently, accurately,y and profitably.
As expectations around sustainability, productivity, and accountability continue to rise, companies that embrace smart equipment management with IoT may be the ones that stay ahead.