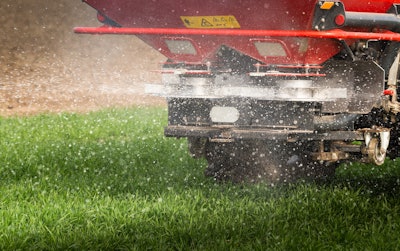
Spreader motors are a vital component of equipment, but their performance and longevity can often be compromised due to harsh operating conditions and maintenance challenges. Small yet impactful changes in design, maintenance practices and technology adoption can dramatically increase the reliability and lifespan of your spreader motors, reducing downtime and repair costs, while boosting user satisfaction.
Here’s everything you need to know to make hydraulic spreader motors last longer.
Identifying the culprits behind motor wear and tear
Understanding the factors that lead to wear and tear in spreader motors provides the foundation for enhancing lifespan. Hydraulic spreader motors, often used in salt spreaders, fertilizer distributors and other and landscaping implements, face several unique challenges.
1. Harsh environmental conditions
Spreader motors are frequently exposed to extreme weather, salt, moisture and corrosive chemicals. These elements accelerate rust, degrade seals and erode internal components, impacting motor efficiency.
2. Operational overload
Overloading motors beyond their intended capacity—whether by demanding higher speeds, excessive force or continuous operation—causes rapid wear to key components like seals, bearings and gear systems.
3. Lack of preventive maintenance
Without regular inspections or servicing, small issues like hydraulic fluid contamination, clogged filters or seal damage can snowball into costly breakdowns. Often, manufacturers underestimate the importance of routine upkeep.
4. Contaminated hydraulic systems
Dirty hydraulic fluid leads to abrasive wear inside the motor, damaging critical components like pistons and gears. This can lead to diminished performance and eventual motor failure. Addressing these challenges requires careful design enhancements and proactive maintenance strategies.
Best practices for extending spreader motor longevity
1. Choose the right materials
Using motors constructed with corrosion-resistant materials, such as stainless steel or nickel-plated components, can reduce the risk of environmental damage. For instance, high-quality seals designed to resist extreme temperatures and chemicals are essential for long-term durability.
Modern advances in materials science are particularly valuable for battling salt and moisture damage in applications like spreaders used during winter de-icing. Testing motors for compatibility with challenging conditions before deployment can also make a significant difference.
2. Optimize load capacities
Make sure the motors properly match their operational demands. Overloaded motors are more likely to overheat, vibrate excessively and break down. Manufacturers can equip machinery with variable speed controls or pressure relief valves to stabilize loads on motors.
3. Develop a maintenance checklist
Implementing a preventive maintenance routine is one of the simplest ways to significantly extend motor life. A robust program should include:
- Regular hydraulic fluid checks: Clean and properly pressurized hydraulic fluid ensures smooth motor operation and prevents internal component wear.
- Inspection of seals and bearings: Replacing worn seals prevents leaks and contamination, while maintaining bearings minimizes heat buildup.
- Filter replacement: Using high-quality filters and replacing them at proper intervals prevents debris from infiltrating the motor.
Remember, the initial startup of any new project is a critical point for catching contamination during break-in. That said, most manufacturers recommend filter replacements within the first 25 hours of use.
4. Leverage predictive maintenance technology
Predictive analytics enabled by internet of things sensors can revolutionize maintenance practices. Sensors installed in spreaders can monitor torque, temperature, vibration data and hydraulic pressure in real time, predicting when components are likely to fail.
This proactive approach allows stakeholders to address issues before they escalate, minimizing expensive downtimes. Many leading manufacturers have already integrated such technology into their equipment lineup.
5. Combat hydraulic contamination head-on
Contaminated hydraulic systems are among the leading causes of motor failures. Ensuring the use of properly filtered hydraulic fluid is vital, as are regular system flushes. Additionally, manufacturers can install wear-resistant motor components that provide temporary resilience against contamination-related wear.
6. Invest in advanced designs
Hydraulic motor engineering has evolved significantly in recent years, offering solutions that address wear and reliability issues head-on. For example:
- Motors designed with low-friction components reduce mechanical stress.
- Systems engineered for self-lubrication can improve performance and lifespan.
By incorporating these advancements into your equipment, you can offer your customers extended value and reliability.
7. Conduct regular training with end users
Even the most advanced designs and maintenance plans will not deliver results unless end-users are trained. Building workshops, digital guides or video tutorials demonstrating correct operation and maintenance practices can empower users to preserve motor quality for the long haul. Doing so will also reinforce your brand as a customer-centric partner.
Technological advances in spreader motor durability
Smart materials and coatings
The development of anticorrosive and self-healing coatings protects spreader motors in corrosive environments, especially those exposed to road salts during winter.
Energy-efficient motors
Hydraulic motors that require less energy to operate generate less heat over time, further enhancing durability.