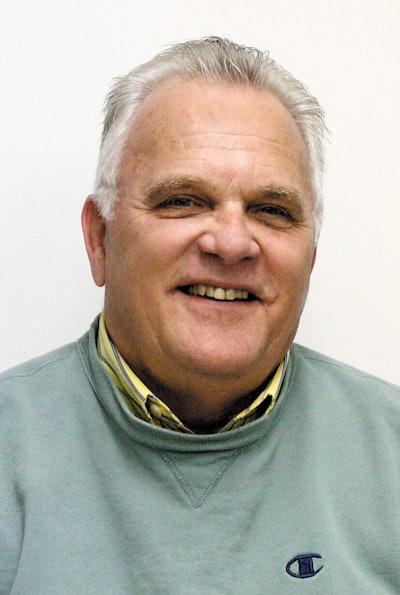
Sometimes OSHA reps ask to visit one of your jobsites or maybe even your facility in order to evaluate your safety initiative. That's why it's important for you and your crews to have adopted an overall culture of safety in your company—and always be prepared for that unexpected OSHA pop-in.
Companies can also take a more proactive approach to an OSHA visit. They can ask to become part of OSHA's Voluntary Protection Programs (VPP). A company first submits an application to OSHA. If chosen, it undergoes a rigorous onsite evaluation by a team of safety and health professionals.
Seeking VPP eligibility requires a major commitment by your company and its employees. But it's a commitment that can pay big dividends over time.
According to an OSHA Fact Sheet, the average VPP business has a lost-workday incident rate at least 50% below its industry average. That leads to direct cost savings, not to mention lower insurance premiums. Additionally, VPP participants are exempt from OSHA programmed inspections while they maintain their VPP status. VPP participants are re-evaluated every three to five years.
Becoming a VPP company can also help you position yourself as a serious, more professional company that does things the right way. This really matters to many of the client types you seek to serve.
Is the landscaping industry up to the task?
It certainly sounds like the pursuit of becoming a VPP company makes a lot of sense. But unfortunately, according to safety expert Dr. Sam Steel, most landscaping companies haven't put themselves in a position to qualify. "In order for a business to be included in the VPP, it must qualify based upon its safety and health management program," says Steel, a senior research associate at Penn State University and PLANET safety adviser.
As Steel points out, there are generally five steps in the safety and health management process:
1. Safety Policies and Procedures. These include individualized and customized business policies and procedures for meeting the requirements of your company's overall safety policies.
2. Safety Risk Management. This includes identification of workplace hazards, and also prioritizing these hazards based on risk level.
3. Safety Program Development. This includes everything from establishing a chain of command and safety program manager to safety committees and safety program resources.
4. Safety Program Implementation. This is the actual delivery of safety programs through training sessions and other educational initiatives.
5. Safety Program Evaluation. This has to do with measuring the effectiveness of your training programs, and then updating and scheduling retraining where problems exist.
"Our Green Industry has developed segments of these steps, but I don't believe we are as far along as other industries," Steel points out. Some other industries, Steel suggests, have better developed this five-step process because of their level of regulation and exposure to government inspections; these industries include airline and maritime, for instance.
"I would also suggest, though, that it has been somewhat of a reactive vs. proactive status that could have prevented some of the hazards that resulted in tragic losses of property and lives (in the landscaping and construction industries)," Steel goes onto say. For instance, "Trenching regulations in the construction industry are examples of life-saving procedures that are enforced by OSHA, but many lives were lost before enforcement began."
To help more landscape companies adopt a more proactive status and develop their five-step safety and health management process, Steel would like to see PLANET be pegged as a Susan Harwood Training Grant Program recipient, much like the Tree Care Industry Association (TCIA) recently experienced. The Susan Harwood Training Grant Program awards grants to nonprofit organizations on a competitive basis. Awards are issued annually based on Congressional appropriation. The focus of the program is to provide training and education for workers and employers on the recognition and prevention of safety and health hazards in their workplaces. Target audiences include underserved, low-literacy, and workers in high-hazard industries.
"It would be a good project for an initial year of funding dedicated to putting our existing resources in place, and then continuing funding to develop the stages in the process that are currently lacking," Steel explains. "Step 5, evaluation, is often the most in need of development."
What OSHA wants when it visits
Short of a Susan Harwood Training Grant coming through, it's not inconceivable that some Green Industry companies do have all five steps securely in place. For those that do and want to learn more about how the OSHA VPP works, OSHA's website offers the following insights.
Once you submit your application and are selected, OSHA will schedule a time to send a team to your site. Once that team arrives and pleasantries are exchanged, it's time to dig right in.
Documentation review. The OSHA team will want to review the documentation of all aspects of your safety and health program. Examples of requested documents include:
- Injury/illness logs
- Workers' comp reports
- First aid logs
- Employee medical records
- Material safety data sheets
- Reports of site inspections and accident investigations
- Emergency procedures
- Safety Committee minutes
- Training records
- Annual evaluation of safety program
Site tour. The OSHA team will also want to tour your site, seeing enough of it to understand the hazards and determine if they are being properly addressed. As you tour, you should note any hazards and suggested improvements that the OSHA team agrees with.
Also during the site tour, it's likely that the OSHA team will want to randomly interview select employees. Typical questions address work procedures, emergency procedures, and personal protective equipment (PPE). Additional, more formal employee interviews may be requested for a time after the site visit is conducted.
Evaluation. At the end of each day, the OSHA team meets amongst itself and also with your company's representatives to discuss its findings. On the final day of the visit, typically, the team decides what its recommendation will be, drafting an initial onsite review report. Recommendations can range from VPP admittance (if everything's in order and all goals are met) to immediate withdrawal (if the company/site's safety and health management program is grossly deficient).
Do you think your company would be admitted or asked to withdraw? By committing to the establishment of a five-step safety and health management process, you certainly make it more likely that you'd be admitted. More importantly, regardless if you participate in the OSHA VPP or not, you'd be making your company a whole lot safer. That's what matters most.