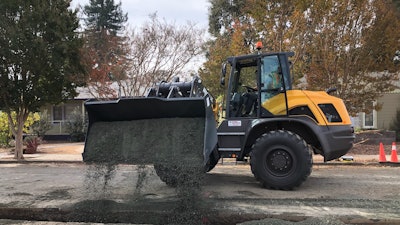
Heavy equipment and other machinery are never inexpensive to purchase. In fact, on average the price for a base model compact tractor is around $10,000.00. With price tags like that, it only makes sense to treat the equipment that you purchase as though it is the only piece of machinery you'll ever buy.
To maintain the life of your equipment, and get all of the hours/miles possible out of your machinery, you need to follow a strict set of guidelines when it comes to the care and use of your machinery.
Commit to A Preventative Maintenance Program
This is more than a simple lube and filter program. Your preventative maintenance program should include items such as component rebuilds, electronic data collection, and a point-to-point inspection program. In other words, ensure that your equipment is handled with the utmost care.
Not only will you see improved equipment reliability and a reduction in unexpected breakdowns, but it will also help your machinery hold its resale value.
Extending the lifetime of your machinery is only one of the benefits that you’ll reap with a comprehensive preventative maintenance program in place. The cost savings you’ll see from major unexpected breakdowns is a huge benefit throughout the healthy lifetime operation of your machinery.
Recognize the Value of Well-Trained Operators
Knowledgeable and thoroughly trained machine operators are often overlooked when it comes to their value. The fact is that a well-trained operator can not only save you costly repairs by recognizing failure early on. They also cause less daily wear and tear to the machinery because they know how to treat the equipment. They can be entrusted with the day to day minor machine maintenance once they’ve been thoroughly trained. This will provide extra savings by reducing the need for maintenance labor to perform routine tasks.
You should try to include operator training in your preventative maintenance program. The tasks that the operator performs regarding maintenance can range from photo-eye adjustments during task changeovers to the daily cleaning and documentation of the machinery. However, all of this is necessary and will ensure that your machinery is being treated in a manner that will allow it to perform to spec for many years to come.
Follow Manufacturers Specifications for Maintenance
The manufacturers of your machinery know it better than anyone else. They not only built the machinery, but they operated and tested the machinery a multitude of times before they ever allowed it to leave the production floor. The owner's manual supplied with your equipment will give you all the factory specifications that need to be followed. Including the frequency with which the machine should have maintenance performed.
When you stick to the manufacturers specifications without fail, you ensure that the machine receives the ideal care. If you allow the machinery to fall behind in preventative maintenance, it’s simply an invitation for a machine breakdown. Something as small as using a non-recommended fluid in the machinery could cause substantial damage and cost you years of machine operation due to that damage. Always follow the manufacturers guidelines for replacement fluids and parts and ensure that the maintenance schedule isn’t deviated from.
Establish A Maintenance Checklist for Operators
When an operator starts a piece of equipment, there are key steps to be taken to use the equipment correctly. A heavy equipment maintenance checklist is a vital piece of tracking data on the machinery. It also ensures all the tasks necessary to properly operate the equipment are performed. And it keeps a record of exactly who performed the necessary tasks at the time. If you are in a facility that uses a CMMS (computerized maintenance management system), this can be done on a computer. Your CMMS will automatically allow reporting on the equipment as soon as it's recorded.
Your heavy equipment maintenance checklist tracks mileage/hours, fluids levels, any visible damage, and the performance of the machinery while in use. This is vital information in the proper maintenance of the machine and can aid in the detection of breakdowns before they become costly part replacements. In addition, it can help to track down operator abuse if there is damage to the equipment. By documenting the precise condition of the equipment at both the start and finish of use, a detailed picture of the equipment performance can be obtained.
Service Records Should Be as Detailed as Possible
When preventative maintenance is performed on a piece of equipment, every tweak and nudge to the machine should be noted. The more detailed the service record, the more complete the picture of the equipment status becomes. When a detailed inspection is performed and the equipment condition is noted, it should include everything from the lights and belts, to the undercarriage and fuel tank.
Cutting edge, tracks or tires, axles, air filters, hoses, and grease lines are all key elements in a properly maintained piece of machinery. The proper documentation of the condition of the machine doesn’t mean only documenting the parts that are having maintenance performed. It should include a full report on the entire piece of machinery from end to end, even if the only maintenance being performed is a lube and filter change. By maintaining thorough service records of the equipment condition, a complete picture of the equipment is painted, and it is much easier to determine where a problem began when breakdowns occur.
Equipment Housekeeping Is Vital
All equipment should be properly cleaned and ready for the next use every time it is returned from an operator. There is no excuse for poor housekeeping, and equipment that isn’t cleaned and properly broken down and stored is equipment that is losing hours and miles from its lifespan. The proper cleaning and storage of all equipment should be a part of the daily operator checklist because it is the responsibility of the operator to ensure that the equipment is returned ready for the next use.
By holding operators accountable for the condition of the equipment when it is returned, you ensure that it is treated with respect and not simply stashed in a dark corner with damage and missing parts. This also prevents modifications from being performed to the equipment that could void warranties and shave down the lifespan of the equipment.
There is no reason that an operator should modify a piece of equipment because the operator should be trained to use the equipment in the manufacturer's recommended condition. This means no engine tweaking or individual adjustments to the machinery that could cause damage or unnecessary wear on the equipment. If the operator cannot use the equipment at manufacturers specification, they simply should not operate that piece of equipment.