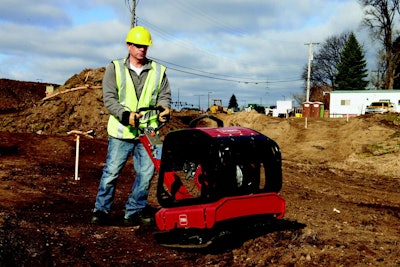
In any given week, landscape contractors have dozens of different tasks to complete. One particular job that is not incredibly glamorous — but is vitally important when it comes to hardscaping and outdoor construction — is soil compaction. This process helps set the foundation for whatever will be going on top of it, whether the contractor is installing pavers, retaining walls, outdoor structures or anything in between.
Sean O’Halloran, marketing manager at The Toro Company, offers the following compaction tips for hardscape and landscape contractors.
Get to know the soil
The compaction process essentially increases the density of the dirt bed, which provides a more stable foundation on which to build. Before selecting the proper equipment, a savvy landscape contractor should consider both soil type and moisture levels. The most common types of soil that a landscape contractor would come into contact during compaction are cohesive (clay) and granular (sand, gravel and silt). In terms of moisture, too much moisture can compromise the integrity of the foundation, and too little moisture can result in poor compaction, as moisture helps the soil granules adhere to one another.
These factors are important in determining whether to use a plate compactor or rammer for compaction purposes. Both offer unique advantages, and are crucial to achieving a solid foundation upon which to work.
Select the right equipment
Rammers are ideal for any soil classified cohesive (clay). The general rule of thumb is that if the soil composition is more than 30% clay, it’s cohesive. Amplitude, which is the maximum movement of a vibrating body from its axis in one direction, is important to consider when determining which compaction equipment will best fit the application. Rammers have higher amplitude than their plate compactor counterparts, which is one of the primary reasons why they do so well in cohesive soil. The repeated impact force essentially forces air and water up and out of the soil beneath.
Rammers have lower vibration frequency when compared to plate compactors, but can generally cover more ground in a shorter amount of time. In this category, there are varying ranges of blows per minute, but Toro rammers can provide anywhere from 650-750 blows per minute, and can exert forces of up to 3,500 pounds. Rammers are easily handled by one worker, and can be transported with relative ease. Additionally, a rammer may be able to fit in tight areas a plate compactor or trench roller would be unable to reach.
What plate compactors lack in ground speed, they make up for with vibration frequency levels. Plate compactors are available in forward-only and forward/reverse models, and can reach vibration levels of 6,000 vibrations per minute. They’re typically bigger and bulkier than rammers, but the increased weight of the machine, and larger surface area contribute to a smoother overall compaction. These machines are ideal for granular soils, as the vibratory nature of the machine encourages particles to fall into a stable position beneath the soil’s surface, eliminating air pockets. Changing direction and even concentrating compaction in one area is simple with most forward/reversible plate compactors models.
Again, it’s crucial for the contractor to first understand the terrain, soil composition and moisture levels before selecting a piece of equipment. Regardless of equipment selection, the operator should make sure to wear approved personal protective equipment (PPE), and take frequent breaks to avoid operator fatigue. Compaction is a lengthy and, at times, complicated process, but with the right equipment, even the most difficult jobs can be handled with relative ease.