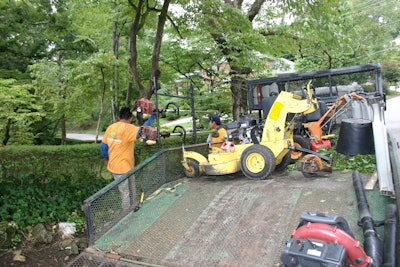
CLASSIC FROM THE ARCHIVES. ORIGINALLY POSTED IN AUGUST 2013 ............................
Jeff Billinger is a branch manager for OneSource Landscape & Golf Services Inc., an ABM Company. He points to several process improvements that have had a positive impact on his lawn maintenance operation's bottom line. One of the biggest is the switch to a four-day workweek.
Fuel savings. Billinger says fuel costs dropped nearly 15% as a result of having to mobilize crews one less day a week. That's due to longer yet more efficient routes, and less time driving to and from the shop.
Here's how it adds up: Let's say a crew burns two gallons of gas per day driving to and from the shop. By not working a fifth day, two gallons of gas are saved each week. Two gallons times 50 weeks is 100 gallons, and 100 gallons times $3.60 per gallon is $360. If you have six maintenance crews, that's $2,160 you're saving on fuel—just by not having to drive to and from the shop one day a week.
Non-billable time. A second area where you'll see savings is in non-billable downtime. "I'm talking about the time spent mobilizing crews in the morning and then demobilizing at night," Billinger says.
Even if you're very efficient and have these times down to 15 minutes per day, they add up to 75 minutes per man per week. By eliminating the fifth working day, you shave that down to 60 minutes. "That's a savings of 8.5 to 13 hours per year per man, depending on how many weeks your crews are working," Billinger points out. If your average employee makes $10 an hour and works 50 weeks per year, it could add up to $125 per year. If you have 20 employees, that's $2,500 right to your bottom line.
If you're like the average contractor whose morning and evening yard times are more in the ballpark of 30 minutes, the savings are even greater. Using the same inputs of 20 employees at $10 per hour working 50 weeks in a year, you could put $5,000 to your bottom line by eliminating a fifth working day.
Controlling overtime. While it's difficult to put a hard number on this, Billinger says the four-day workweek is an effective management tool to control overtime. "We start at 6:30 a.m. and work until 5 p.m. to get our 10 hours per day in," Billinger says.
Crews work Monday through Thursday. Some companies prefer Tuesday through Friday, saying that some customers demand their presence on Fridays. Other companies like to stagger crews so at least one is working every day. "We prefer Monday through Thursday because that leaves Friday as a rain day," Billinger says. This is an advantage, especially when servicing residential accounts since they usually don't want you there on the weekend.
Employee morale. Billinger says crews have responded well to the four-day workweek. One benefit is that they get to enjoy a three-day weekend to either relax or work a part-time job. They also save a day's worth of gas driving to work, and in some cases a day's worth of day care.
Managers continue to work that fifth day on Friday. "This gives them a great opportunity for planning or catching up on paperwork and proposals," Billinger says. "We also have our production meetings on Fridays to review the past week and plan for the coming week. By having these meetings on Fridays, we don't have to pull the managers and supervisors out of the field away from their crews and sites."
Mechanics also like having the crews off on Friday as it gives them a day to service vehicles and equipment without having to take them out of production.
Decrease in absenteeism. Finally, the four-day workweek has resulted in a decrease in absenteeism. Employees now have Fridays to run their personal errands. Friday is also a more opportune time for managers and supervisors to take personal days off, since they won't miss being in the field with crews.