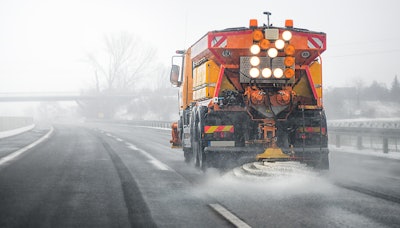
When it comes to spreading and spraying to manage ice, there’s always room for improvement, but where to start? Years of experience in the industry and working with contractors from across the country has shed light on some of the most common mistakes and areas for improvement. Whether you’re a seasoned contractor or new to the industry, making some of these small changes can have a big impact on the bottom line. Here are ideas on what you should—and shouldn’t—be doing in your ice management operation.
1. Preseason preparation
Don’t: Wait until the last minute.
Too many contractors wait until the last minute to pull their snow and ice management equipment out of storage. Just because it worked when it was put away doesn’t mean it will work at the start of a new season. Batteries could be dead, electrical connections could be corroded or moving parts could be seized. Discovering these issues right before a snow event occurs is the perfect storm for disaster.
Do: Thoroughly check equipment well before the season starts.
It’s important to run through equipment well in advance of when it will be needed. Contractors should have a detailed preflight checklist of sorts to ensure everything is set up for success. Be sure to include the following items:
A. Subscriptions: If any subscriptions are required for running equipment or managing operations, make sure they haven’t expired.
B. Spinners: Make sure they spin freely. If they don’t, it could suggest an issue with the gearbox.
C. Augers or conveyors: Run these components without material in the hopper to make sure they operate properly without any unusual noises. Conveyor drives require more maintenance than augers. Operators need to ensure sprocket alignment, pintle condition and chain tension on these systems.
D. Electrical connections: Check for corrosion and apply new dielectric grease on all electrical connectors.
2. In-season maintenance
Don’t: Ignore maintenance during the season.
After working long hours during a winter event, maintenance is often the last thing anyone wants to do. As a result, many people simply park their trucks until the next storm comes. However, skipping minor maintenance tasks could snowball into major issues down the road.
Do: Maintain equipment after each use.
Spreaders should be cleaned thoroughly with water after each use. Especially take care to rinse the bottom of the trough and run the auger or chain with the hopper empty. Otherwise, any remaining salt in the unit could freeze solid and prevent the spreader from working properly the next time. Breaking up frozen rock salt isn’t much different than busting concrete blocks. If an operator tries to run an auger or conveyor that’s seized up in frozen material, the controller could throw a code or blow a fuse. Or worse, the controller could fry.
Liquid systems should also be flushed with water to help prevent any residual salt from damaging the pump, seals and other components. After flushing with water, be sure to run antifreeze or windshield waster fluid through the system to prevent freezing, while offering some lubrication value to the pump.
In addition to washing the equipment, be sure to check the bolts, apply the recommended grease and provide an overall inspection.
3. Material management
Don’t: Preload your equipment with salt.
Too often this basic piece of advice is ignored. Many contractors try to save time by loading their spreaders with salt way before a storm hits, but what happens is the salt will draw in moisture and freeze while it sits idle, and the equipment will jam. In the end, trying to save 10 minutes by pre-loading equipment can turn into several hours unloading the spreader to clear the frozen material.
This advice applies to sprayers as well. Even though brine has a low freezing point, the material sitting in the lines may still freeze if the vehicle is left outside. The large volume of brine in the tank will likely be fine, but the stuff in the hoses, surrounded by frigid air, will ice up quicker, similar to how ice forms faster on bridges than the rest of the road.
Do: Ensure your material supply.
A good rule of thumb is to keep enough material on hand for two or three successive storms. Also, have a plan in place to get resupplied when that runs out. Remember that in an active winter season with multiple snow and ice events, material costs often increase as more people scramble to shore up supply.
As a result, it’s important to have discussions with vendors and agree upon pricing before the season begins. This step can help protect yourself from spreading material that costs more than what you can charge clients.
4. Calibration
Don’t: Skip calibration.
Calibration may be an even less popular job than equipment maintenance, but it’s highly important. Although it takes time and can get messy, it’s imperative toward understanding exactly how much material is being applied on each job.
Far too many contractors set their controller dials to the same number each time they go out on a job, simply because it seems to be putting down a decent amount of material at that setting. At the end of the day, however, they don’t know exactly how much material is being spread at a “5” or “7” on the dial. And that means they don’t have a true grasp on profitability, nor do they have proper documentation for defending themselves against slip-and-fall claims.
Do: Calibrate equipment often.
Whether they do it or not, many contractors understand the reason for calibrating spreaders each time they change material, since each material spreads differently due to variances in density, but did you know it’s best to calibrate spreaders each time they’re used, even if the type of material stays the same? That’s because the density of material changes throughout a salt pile as it gets worked down throughout the season. Not accounting for small differences like this can result in big miscalculations over time when spreading large amounts of material.
Sprayers should be calibrated often, too, although it’s not as big of a concern since a supplier’s brine should be consistent from one batch to another. However, be sure to calibrate using the actual product in winter weather conditions. Calibrating in warm temperatures with water will provide inaccurate results, due to differences in density and changes in viscosity from warm to cold temperatures.
Fortunately, equipment manufacturers understand the frustrations with calibration, so they’re designing controllers to make the process as easy as possible. More sophisticated spreaders on the market have controls that go beyond the traditional numerical dial settings, allowing operators to instead enter how many pounds of material per square feet they wish to apply. As drivers speed up and slow down on the job, the controller will automatically adjust the auger or conveyor to achieve the exact target rate on the property.
5. Innovation and adaptation
Don’t: Resist change.
The winter maintenance industry is changing fast. Technology improvements, labor shortages, environmental trends and legislative challenges are just a few examples of things that are drastically different now than they were just 10 years ago. Like them or not, it’s important to adapt, because those who refuse to put in the effort could struggle being in business another 10 years from now.
Do: Learn as much as you can.
Strive to be an expert in your field. This applies to all areas of the business, from equipment, technology and materials to overall operations management. For example, don’t simply purchase a piece of equipment because a buddy recommended it. Research all the options yourself, knowing their capabilities, strengths and weaknesses, and then purchase products that are best for your operation.
Additionally, understand all available de-icing materials to know which products to use in various conditions. And research the latest technologies that can increase efficiency and improve service. After all, the most successful contractors are generally the ones who know their business the best and embrace technology the most.
The purpose of this advice is to help make sure you don’t lose money in this industry and that you do become successful. By avoiding most of the common mistakes made by contractors, while proactively taking steps to improve your operation, you’ll be well on your way to being a top winter maintenance contractor in your area.