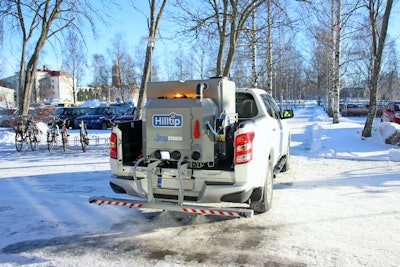
Municipal leaders, engineers, snow and ice equipment manufacturers, climate scientists and truck operators nationwide work together to create and implement solutions to effectively clear roads and walkways and keep residents safe, notes Andy Holverson, Monroe Truck Equipment general manager, municipal division.
One snow and ice management solution is liquid anti-icing.
The technique has been around since the 1990s, but has only recently been widely adapted by communities nationwide, says Holverson.
Anti-icing materials are liquid brine products applied to dry pavement before a winter storm to help prevent ice formation when the storm occurs, notes Craig Sandmann, Hilltip North America managing director.
The liquids are made from the same materials used for over-the-top de-icing applications; the only difference is how they are applied, he says.
Anti-icing chemicals are used to prevent ice from forming and bonding to the surface. De-icing chemicals remove ice that has already formed on the surface, notes Seth Bergerud, senior product manager, Douglas Dynamics.
“A thin layer of liquid chemical compound—often liquid sodium chloride—is distributed on the street prior to a snow event,” Holverson says, adding that anti-icing prepares the ground to reject bonding to snow and ice.
The technique enables municipalities to proactively reduce the amount of labor and materials needed to clear an area and is a way to better protect drivers and pedestrians as they travel during or after a snow storm, he adds.
Many companies offer technology that allows snow professionals to accurately calibrate their spray equipment.Hilltip Corp.
Common anti-icing materials
Sodium chloride, a basic solution of rock salt and water, is the most common and cost-effective type of brine used for anti-icing, says Sandmann.
“However, it is not recommended for all uses," Sandmann says. "Extreme cold temperatures, environmentally sensitive sites and other situations may warrant the use of different products.”
Other anti-icing materials include calcium chlorides, potassium acetates, magnesium chlorides, alcohol distillates and carbohydrate-based solutions.
Sodium chloride is used in bulk granular form and spread on surfaces or dissolved into water to form brine that can be sprayed on surfaces, says Bergerud. Sodium chloride dissolved into water absorbs energy in the form of heat from the environment—an endothermic reaction, he adds.
“The resulting solution—salt brine—has a lower freezing temperature than water,” says Bergerud. “By staying in liquid form at a lower temperature, it prevents ice from bonding to road surfaces.”
Calcium chloride and magnesium chloride also dissolve into water to create a brine.
“But when their crystalline structure breaks down in this process, the reaction gives heat off, an exothermic reaction,” says Bergerud. “They are more effective at lower temperatures than sodium chloride and are essential in dealing with very cold temperatures common throughout the North American snowbelt. They are often used as an additive to supplement the effectiveness of sodium chloride.”
Potassium-based chemicals are used in anti-icing where corrosion from traditional salting is not acceptable, he adds.
Airports, parking structures and other sensitive surfaces may require these types of special materials, Bergerud says, adding they are much less cost effective than chlorides.
The upsides
As a liquid solution, anti-icing requires less material to be effective over longer lengths of road, notes Holverson.
“By preventing bonds from forming before the storm, it takes fewer workers less time to remove snow and ice,” Holverson says, adding state transportation departments can use labor cost savings for other areas of need.
While rock salt can quickly bounce and scatter across the road, reducing efficacy, liquid solutions are sprayed and can generally stay in place, ensuring the application area can reduce bonding, Holverson says.
“The less granular salt needed, the less material is displaced by high traffic or slopes in the roads that eventually lead to waterways,” Holverson says of the environmental benefits.
One of the biggest steps to anti-icing success is to monitor input costs.
“Material is one of a contractor’s biggest expenses, so managing it wisely is imperative to profitability,” Sandmann says. “Under- and over-applying liquids can both negatively impact the bottom line.”
Today’s sprayers and control systems help ensure the exact amount of material is applied on each jobsite and provides needed documentation for billing and business management purposes, Sandmann notes.
Best management practices
It is common to apply anti-icing materials up to 48 hours in advance of expected icing conditions, says Bergerud.
“Brine or liquid treatments have the advantage of being applied and allowing the water to evaporate, leaving a thin layer of crystalized salt on the surface,” Bergerud adds. “Treating the surface in advance of a storm ensures safer conditions should a storm arrive early, and also allows the first snow to melt on contact, buying time for plow trucks and salting trucks to clear the surface.”
In applying anti-icing materials effectively, contractors should have a good understanding of all anti-icing products available as well as the effective temperature ranges and appropriate application rates for each one, says Sandmann.
Contractors should closely monitor weather conditions, which greatly influence anti-icing decisions, he adds.
A well-calibrated anti-icing sprayer is key to ensuring correct material rates are applied. Using advanced sprayers and controller systems also helps maximize application accuracy and efficiency.
Bergerud says while anti-icing materials can be applied at any time, the common practice of applying them 24 to 48 hours in advance of the storm allows equipment operators to work during normal working hours and has the advantage of the warmth of the day to help evaporate brine when applied. It also reduces overtime and after-hours work when labor costs are at a premium.
“It also improves the efficiency of snow removal (plowing) by preventing ice from bonding to the surface and creating hardpack that requires additional material to melt and remove,” Bergerud says.
Sandmann adds that air and surface temperatures are major factors in deciding which materials to use and how much to apply.
"If a storm is expected to hit in several hours with expected temperatures ranging from 20 to 32 degrees Fahrenheit, then an appropriate rate of calcium chloride may be a cost-effective solution," Sandmann says. “If, however, the temperature will range from 0 to 15 degrees, then calcium chloride won’t work as well. Magnesium chloride would likely be a better choice.”
Cost and safety considerations
Addressing anti-icing materials costs compared to traditional snow removal methods, Sandmann says many contractors experience reduced material costs, especially when best practices and proper application rates are followed.
“The biggest benefit to anti-icing is not necessarily reduced costs, but improved safety by preventing ice from forming on the surface,” Sandmann says. “Additional savings occur during the actual plowing of accumulated ice and snow on treated areas because the bonding of ice with the pavement is less effective, making it faster and easier to remove.”
Bergerud adds that despite the best predictive technology, weather forecasts are never perfect.
“By preparing in advance of the storm and applying anti-icing materials to the surface, operations teams have a wider window of time to deploy and road surfaces maintain safe driving conditions longer by preventing freezing and hardpack in early snow," Bergerud says.
By preventing ice from forming on surfaces, contractors can greatly reduce the possibility of an accident between the time a storm begins and when the contractor returns to the site to manage the snow and ice, says Sandmann.
“Any ice that does form on a surface can be removed more easily since the bond between the ice and surface isn’t as strong, resulting in a cleaner surface,” Sandmann says.
Sandmann notes chemical suppliers can provide recommendations on which materials to use and how much to apply.
Bergerud advises snow professionals to secure a source for purchasing brine or the equipment and expertise to manufacture brine. Liquids application equipment also must be sourced. Operators must be trained on their effective use in all wide-ranging weather conditions.
Training for effective results
Holverson notes there are logistical hurdles to mastering the use of liquid anti-icers, with there being a dynamic between temperature, timing and the solution created.
“Depending on the liquid solution you choose, you may have to pay attention to the temperature of the pavement when you’re anti-icing,” Holverson adds. “Certain liquids have more strict requirements than others.”
Calibration depends on the liquid spreader being used and the area needed to be covered, Holverson says, adding the Clear Roads Technical Advisory Committee has helpful information.
Workers need to learn how to safely handle the liquid material chosen and should be provided a Material Safety Data Sheet, Holverson notes.
A municipality adapting anti-icing techniques may not have the amount of equipment or materials needed to treat their entire community before a storm, says Holverson.
Consider traffic volume, traffic speed, important bridges, and residential or institutional density to deliver treatment to the areas that most need it, he adds.
Liquid anti-icers need completely different storage and distribution equipment than granular de-icers, Holverson notes.
“Instead of spreaders, you need tanks, nozzles and pumps,” Holverson says. “You don’t need to replace your entire fleet of plows and spreaders. Investing in a few anti-icing trucks or trailers can make an incredible difference for your budget and community.”
Most industry organizations are promoting the use of liquids with increased education, says Sandmann.
“Many contractors who have successfully implemented anti-icing services are willing to share their knowledge and experience at industry events,” Sandmann says. “Other options are to research anti-icing on the internet, connect with other professionals on social media groups, and tap into equipment and chemical dealers for advice on proper application of anti-icing liquids.”
Equipment manufacturers provide manuals, videos, and other training materials supporting their equipment use, says Bergerud.
“Trade organizations such as the Snow and Ice Management Association (SIMA), consultants and peer groups such as Snow Fighters and local groups all offer materials to help professionals share best practices and build competencies and mastery of very challenging work in the most difficult conditions,” Bergerud says.
Regulatory considerations
Sandmann notes most current and proposed regulations focus on reducing the amount of salt used for snow and ice management due to environmental concerns.
“Using liquids for pre-wetting, as well as anti-icing, is the only proven way to reduce salt usage while continuing to effectively deal with snow and ice,” Sandmann says.
Regulations around chloride usage continue to evolve, says Bergerud.
“Predominantly, these have been introduced at the local and state level,” he says. “New Hampshire and Minnesota are leaders in this space. Other states are following with similar legislation.”
Trends and technologies shaping the future
Sandmann notes present-day anti-icing sprayers are highly accurate and reliable, and some controllers can practically automate the process while removing the guesswork. Reports showing how much material was applied on each jobsite and weather conditions help minimize liability, and some controllers have two-way GPRS technology allowing managers to monitor drivers from a smartphone, tablet, or computer, Sandmann says.
“Equipment settings can be viewed and modified remotely to ensure jobs are getting completed properly,” Sandmann says. “Geofencing technologies allow properties to be mapped out.”
Bergerud says as costs come down for sensor technology, computing power, and data storage, better solutions will continue to evolve.
“Anti-icing has become commonplace in many European countries, and North America is likely to follow suit as contractors become more concerned with minimizing liability and reducing their environmental footprint,” says Sandmann. “However, most contractors in the U.S. still don’t offer this service. Those who start now can gain a competitive edge.”