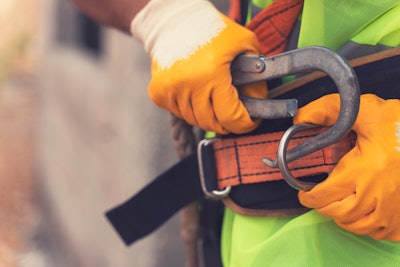
The Occupational Safety and Health Administration (OSHA) recently released its preliminary list of the 10 most frequently cited safety violations from the 2022 fiscal year.
For most contractors, the list serves as a reminder that risks and violations continue to challenge businesses that don’t follow thorough safety practices. But more importantly, it can help you identify and address safety gaps that might exist on your jobsite. For the purpose of this article, I’ve included both construction and general industry standards, however, you can sort violations by industry on OSHA.gov.
Let’s take a closer look at each violation on OSHA’s list, and the reminders they provide.
1. Fall Protection: General Requirements (1926.501)
Fall protection general requirements topped OSHA’s annual violations list for the 12th straight year. Unfortunately, fall protection—or lack thereof—has become more than just a hazard. Falls are one of the leading causes of occupational fatalities, particularly in the construction industry.
Reminder: Provide personal protective equipment (PPE), along with guardrails, safety nets or fall arrest systems for employees above 6 feet or more. Train your team on the proper use of fall protection equipment and inspect your systems regularly.
2. Hazard Communication (1910.1200)
Employees have the right to know about any hazardous materials they may work with and how to handle them. Hazards can range from gases and vapors to fumes, fibers, and mist. And as the second most cited violation on OSHA’s list, there’s plenty of room for more hazard communication.
Reminder: Inform workers of hazardous chemicals, the risks associated with exposure and safety measures. Share this information with your employees through written programs, hazard labels and warnings, safety data sheets (SDSs) and in-person training.
3. Respiratory Protection (1910.134)
Like hazard communication, respiratory protection standards can help protect workers from harmful substances and air pollutants. Still, many businesses over the past year struggled to obtain proper medical evaluations, provide fit testing to their employees or implement respiratory protection programs.
Reminder: Equip your employees with the appropriate respirators and educate them on proper uses. Create a formal respiratory protection program that requires employees to complete medical evaluations, perform fit testing, and participate in respirator training.
4. Ladders (1926.1053)
Ladders are an invaluable tool on most worksites, but they can present several hazards for those using them. The results of improper use can lead to serious injury—and, as seen by OSHA’s list—result in penalties.
Reminder: Inspect your ladders and remove broken or poorly maintained items from service. Evaluate how much weight your ladders can support and train employees on proper usage. Remind your team to avoid standing on the top step (or cap) of ladders.
5. Scaffolding (1926.451)
As projects progress, scaffolding is often modified or altered to complete tasks. Because of this, it can be easy for teams to overlook the proper fall protection, safe access and planking requirements necessary to keep workers safe, which is why scaffolding hazards rounded out OSHA’s top five most cited violations.
Reminder: Ensure your scaffolding is safe, sturdy, and able to support its own weight, plus four times the total maximum intended load. Review the full OSHA standard to ensure your scaffolds align with requirements for weight limitations, planking, and decking. Inspect and remove damaged pieces from service.
6. Lockout/Tagout (1910.147)
Nearly every contractor relies on energized machinery to keep projects moving forward. Unfortunately, the hazardous energy within machinery can injure or kill workers if it’s released during maintenance work. Lockout/Tagout (LOTO) procedures can help protect workers, but only if they’re implemented properly. If not, businesses may face violations and put their workers at risk.
Reminder: Identify your machinery’s hazardous energy sources and develop machine-specific LOTO procedures. Train your team on how to deenergize equipment and apply LOTO devices.
7. Powered Industrial Trucks (1910.178)
With so many materials to move around jobsites, many businesses use forklifts or lift trucks for transporting items. But such large machinery can add risk if untrained or inexperienced drivers get behind the wheel.
Reminder: Provide classroom and practical training to workers who operate forklifts and other heavy machinery on your worksite. Ensure each operator has the proper certification and recertification needed to drive.
8. Fall Protection: Training Requirements (1926.503)
The topic of fall protection made OSHA’s list twice—this time for training violations. If you’ve sensed a theme so far, it’s that safety starts with training. Informed, well-trained workers can help manage and reduce risks, particularly in an industry working above ground.
Reminder: Provide fall protection training to all employees who may work at heights on your jobsite. Conduct a fall hazard assessment to identify areas and responsibilities that expose your team to fall hazards.
9. Eye and Face Protection (1926.102)
Construction work often involves tasks near flying particles, hazardous chemicals and other debris—all of which can lead to eye injuries. Although eye injuries are among the most preventable occupational injuries, many businesses received violations for not providing or requiring proper eye protection.
Reminder: Assess your PPE hazards and provide proper equipment for the eye and face exposures your workers face. Eye protection options include safety glasses, safety goggles, face shields, welding helmets, laser-safe lenses and prescription glasses or goggles. Provide adequate training to your team and ask supervisors to monitor the use of PPE around hazards.
10. Machine Guarding (1910.212)
When used correctly, machinery can help expedite tasks and keep project timelines on track, but without caution and safeguards in place, employees who operate or maintain machinery could risk severe injury.
Reminder: Identify workplace machinery that may cause injury to your workers at the point of operation, from rotating and moving parts or flying chips and sparks. Once you’ve identified these risks, perform machine-guarding assessments on the equipment and install guards as needed.
The Takeaway
As a safety services manager for Sentry, my team and I have worked with hundreds of businesses, and after countless visits, one quality stands out among the most successful contractors: those who embrace safety and reduce work-related injuries.
Each of these standards can help you assess and update your existing workplace safety program—but they don’t capture every risk or compliance standard that could lead to an injury. For example, trenching and excavation safety is a common risk facing most contractors and a standard that sees some of the most frequent citations within construction. For the most recent guidance, I encourage you to visit OSHA.gov.
You can also talk with your insurer or local expert for safety policies specific to your business. By complying with OSHA standards, you may even lower your overall workers’ compensation costs by reducing or preventing workplace accidents over time.