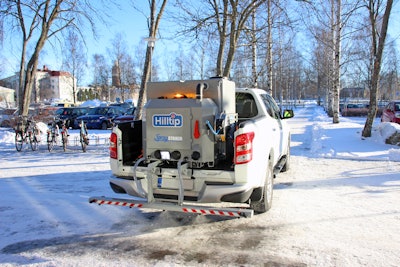
Although prewetting, anti-icing and liquid de-icing are commonplace throughout Europe today, winter maintenance professionals in North America have been relatively slow to embrace the technology. However, according to many experts, it’s only a matter of time before liquids become the norm here, too.
Of course, most winter maintenance contractors are taking the safe approach. They’re waiting to make sure enough other people are using liquids successfully before making the leap themselves. However, the resources and equipment technologies available today can make the transition easier than most would imagine. Plus, those who implement liquids now could gain a strong advantage over competitors who drag their feet. All it takes is a little liquid courage, so to speak.
The benefits
By now, most contractors are aware of the benefits of prewetting, anti-icing and de-icing. The biggest one is that salt costs can be reduced significantly. In fact, a 30 percent reduction in salt use is a realistic expectation at minimum. The majority of contractors probably save closer to 40 or 50 percent. In the right environment, some people have even saved up to 75 percent by wisely managing their liquids. The money saved on material can go directly to the bottom line.
When used correctly, liquids can increase the effectiveness of snow and ice management programs.Hilltip Corp.
Finally, liability reduction is the other main driver for using liquids. In our highly litigious society, we’re forced to manage snow and ice as effectively as possible or risk facing a lawsuit. Used properly, liquids can increase the effectiveness of a winter maintenance program, helping to reduce legal exposure.
The roadblocks
The benefits sound great, but there are obviously reasons why everybody’s not doing it yet, beyond waiting for others to implement liquids first. Roadblocks do exist on the path to liquid ice management, but they’ve gotten much easier to navigate in recent years.
For instance, many contractors aren’t sure how to actually get brine. Many assume they have to make it themselves, but then they see the cost of brine equipment and decide against it. Not to mention, making brine requires additional know-how and special licensing.
However, the best approach for most people is to purchase brine from chemical companies who know what they’re doing and have reliable manufacturing capabilities. In the end, contractors may come to appreciate the convenience of buying and storing brine in totes from their suppliers.
A bigger roadblock may simply be a lack of confidence in using liquids, despite increased awareness about prewetting, anti-icing and de-icing. Various factors, such as ambient temperatures, ground temperatures and weather forecasts, can affect the application and type of liquids used. The set of considerations are somewhat different than rock salt applications, so a certain amount of education is needed to do the job right.
Luckily, that education is getting easier to find through online resources, professional associations and even governmental agencies. For instance, the New Hampshire Department of Environmental Services offers “Green SnowPro” certification with the goal of mitigating salt usage.
An often-overlooked resource is the brine supplier, which is another great reason to purchase brine instead of making it. Representatives from these companies have tremendous chemical knowledge. They can recommend exactly what liquids should be applied in each condition, helping give contractors the confidence they need to effectively use liquids.
Another common roadblock in the move to liquids is how to bill for it. Contractors can often overcome this by remembering what exactly the client is paying for—a clear parking lot. The materials used are not of concern to them as long as expectations are met or exceeded. As a result, contractors can confidently bill the same amount for a job even if fewer materials are used to adequately service the property.
The competitive advantages
Despite its perception as a roadblock, billing should actually be considered an advantage to contractors who offer prewetting, anti-icing and liquid de-icing. Many clients would be happy to pay for services that are more environmentally friendly—especially if they work more effectively without costing significantly more.
Winter maintenance professionals wanting to leverage the green aspect even further can benefit from the latest electric-powered equipment offerings. For instance, high-flow brine sprayers have traditionally been powered by engines or hydraulics. Small engines, of course, produce harmful emissions, negating some of the environmental benefits of liquids. Not only do hydraulic-powered sprayers require expensive central hydraulic systems, but the vehicle also consumes more fuel to run the hydraulics.
Today, manufacturers have developed high-flow sprayers that are completely electric powered. Using 12- or 24-volt systems that run off the vehicle’s electrical system, these sprayers can produce as much output as engine- or hydraulic-powered ones. This provides yet another selling point to clients who are sensitive to environmental issues and looking to reduce their carbon footprints as much as possible.
Additionally, advanced controls can help increase efficiency even further on some of the latest sprayers. For instance, software like tracking systems allow contractors to enter desired application rates for each jobsite using a computer, smartphone or tablet. As a driver enters each jobsite, the controller uses GPS positioning to recognize its location and load the preset application rates. Then, the operator can simply drive, and the equipment will automatically adjust the sprayer flow according to the vehicle speed in order to achieve the desired material rate for that property. This capability helps save salt by preventing over-application and, in the end, the contractor knows exactly how much material is used on each property. The controller will also record all important jobsite data, providing documentation for use in billing or slip-and-fall disputes.
Thanks to these advancements in equipment and greater availability of educational resources, contractors are running out of excuses—and time—to be on the forefront of liquid technology. Sooner or later, brine will be adopted by many more people in North America, just as it has been in Europe. And, once again, the playing field will be level when the majority of contractors start prewetting, anti-icing and de-icing. In the meantime, there’s still opportunity to get some liquid courage…and start gaining your competitive advantage.